Why Rotomolding is the Preferred Choice for Heavy-Duty Applications
Why Rotomolding is the Preferred Choice for Heavy-Duty Applications
Blog Article
Rotational molding, frequently known as Plastics Rotomolding, is an essential method in industrial plastic production, enjoying a significant role in making sturdy, top quality services and products across numerous industries. That production method has been embraced because of its capacity to make intricate, empty plastic products which are equally effective and light, rendering it a go-to process for a wide selection of industrial applications.
What Makes Rotational Molding So Essential?
Rotational molding presents unique benefits around other plastic production processes. Unlike injection molding or strike molding, rotomolding involves heat plastic resin in a very mold, while rotating it along multiple axes. This technique results in a straight layer of plastic on the inner floor of the mold, enabling uniform width and a smooth finish.

This unique process is specially valuable in industries where durability, energy, and resistance to use and grab are crucial. Rotational molding is great for making big, useless areas such as for instance storage tanks, bins, and pots, along with smaller stuff like automotive components and underwater products. Their ability to produce easy, durable products with large impact opposition assures that these things may endure severe conditions, making them fundamental in industries like agriculture, construction, and logistics.
Critical Great things about Rotational Molding
Among the standout advantages of rotational molding is its mobility in design. The method may accommodate complicated designs and different wall thicknesses, letting producers to meet up precise design specifications. Additionally, the absence of joints or weld lines increases the power and durability of the merchandise, reducing possible fragile spots that could lead to failure below stress.
Rotational molding also helps the utilization of a wide variety of components, giving suppliers more possibilities as it pertains to selecting the right plastic for his or her needs. Whether it's a very durable material for heavy-duty programs or a light choice for consumer things, the flexibility of this technique helps appeal to varied manufacturing needs.
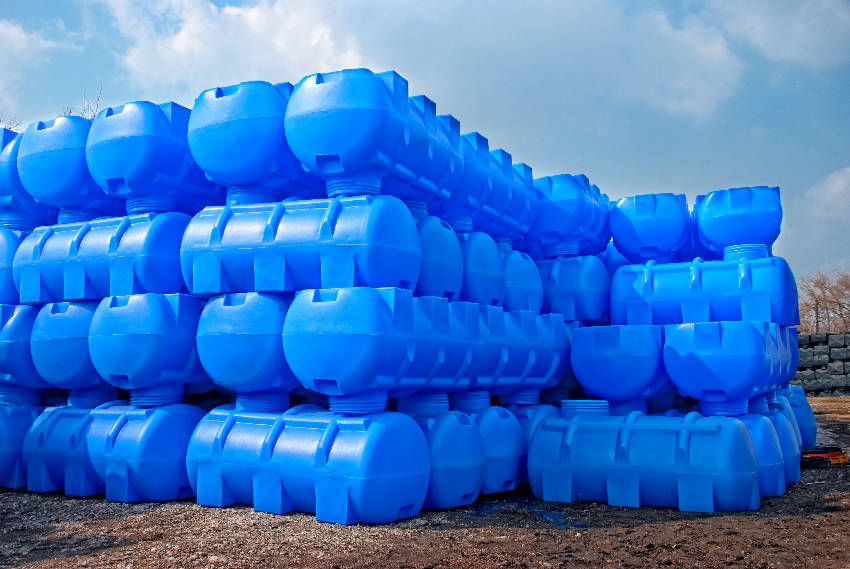
Sustainability and Cost-Effectiveness
Another key benefit could be the sustainability facet of rotomolding. The method yields small spend because excess product can frequently be recycled and reused in potential creation runs. Moreover, the energy-efficient character of rotational molding helps it be a cost-effective choice for large-scale manufacturing, letting companies to steadfastly keep up aggressive pricing while still achieving top quality results.
Conclusion
Rotational molding is a cornerstone of commercial plastic creation, giving advantages that go far beyond simple manufacturing. Their ability to create durable, variable, and cost-effective plastic products with small spend helps it be a vital process for many industries. As commercial requirements keep on to develop, the significance of rotational molding in providing trusted, sustainable solutions will only raise, solidifying its position as a key technique in modern manufacturing. Report this page